Understanding Push Back Racking: A Space-Saving Storage Solution
In modern warehousing, maximizing space and improving efficiency are critical for businesses aiming to streamline operations. Push Back Racking is an innovative storage system designed to optimize warehouse space while maintaining accessibility to stored goods. This article explores what Push Back Racking is, how it works, and its key benefits for warehouses.
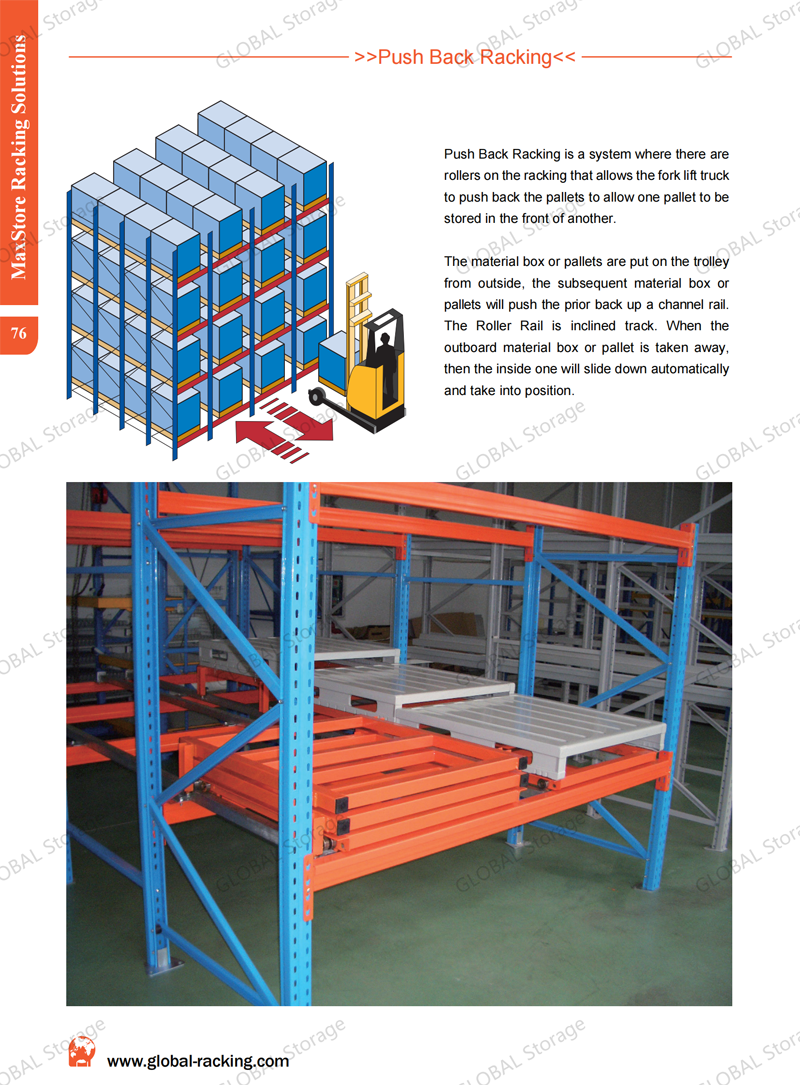
What is Push Back Racking?
Push Back Racking is a dynamic storage system that allows multiple pallets to be stored in a single lane, utilizing inclined rails and carts to facilitate easy loading and unloading. Unlike traditional selective racking, which stores one pallet per position, Push Back Racking enables pallets to be stored up to six deep on each level. This high-density storage solution is ideal for warehouses with limited space or those handling a large number of SKUs (Stock Keeping Units).
How Does Push Back Racking Work?
The system operates on a Last-In, First-Out (LIFO) inventory management principle. Pallets are loaded onto carts that slide along inclined rails within the rack structure. When a new pallet is added, it pushes the existing pallets backward along the rails. To retrieve a pallet, operators simply remove the frontmost pallet, and the remaining pallets slide forward automatically due to gravity. This design ensures smooth and efficient access to goods without the need to enter the racking structure.
Key Benefits of Push Back Racking
Maximized Space Utilization: By allowing multiple pallets to be stored in a single lane, Push Back Racking significantly increases storage density compared to traditional racking systems.
Improved Accessibility: Despite its high-density design, the system ensures that pallets remain easily accessible, reducing retrieval times and boosting operational efficiency.
Versatility: Push Back Racking is suitable for a wide range of industries, including food and beverage, manufacturing, and retail, accommodating various pallet sizes and weights.
Enhanced Safety: The system minimizes the need for forklifts to enter the racking structure, reducing the risk of accidents and damage to goods.
Cost-Effective: By optimizing warehouse space, businesses can delay or avoid costly facility expansions while maintaining high storage capacity.
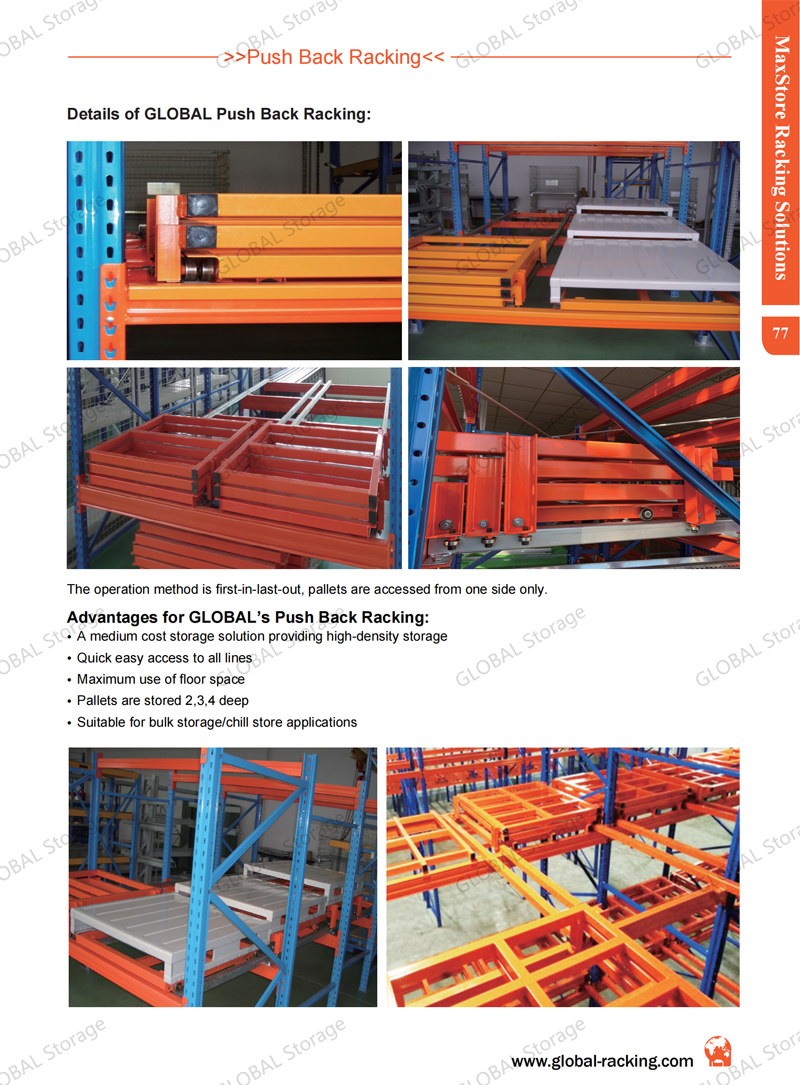
Applications and Considerations
Push Back Racking is particularly effective for businesses with high-volume inventory and a need for efficient space management. It is commonly used in cold storage, distribution centers, and facilities with fast-moving goods. However, since it operates on a LIFO basis, it may not be suitable for products with strict expiration dates, such as perishable goods, unless inventory is carefully managed.
When implementing Push Back Racking, businesses should consider factors such as pallet weight, forklift compatibility, and warehouse layout to ensure optimal performance. Consulting with a storage solutions provider can help tailor the system to specific operational needs.
Push Back Racking offers a practical and efficient solution for warehouses looking to maximize space without sacrificing accessibility. Its innovative design and versatility make it a valuable asset for businesses aiming to enhance productivity and reduce costs. By adopting this system, companies can achieve a more organized, space-efficient, and safe warehousing environment.
To know more please contact us.Email:[email protected]