Drive In Racking System: An In - Depth Look at High - Density Storage Solutions
In the dynamic world of modern warehousing and logistics, the optimization of storage space and the enhancement of operational efficiency are constant pursuits. The Drive In Racking System has emerged as a game - changing solution, especially for businesses dealing with homogeneous products in large quantities.
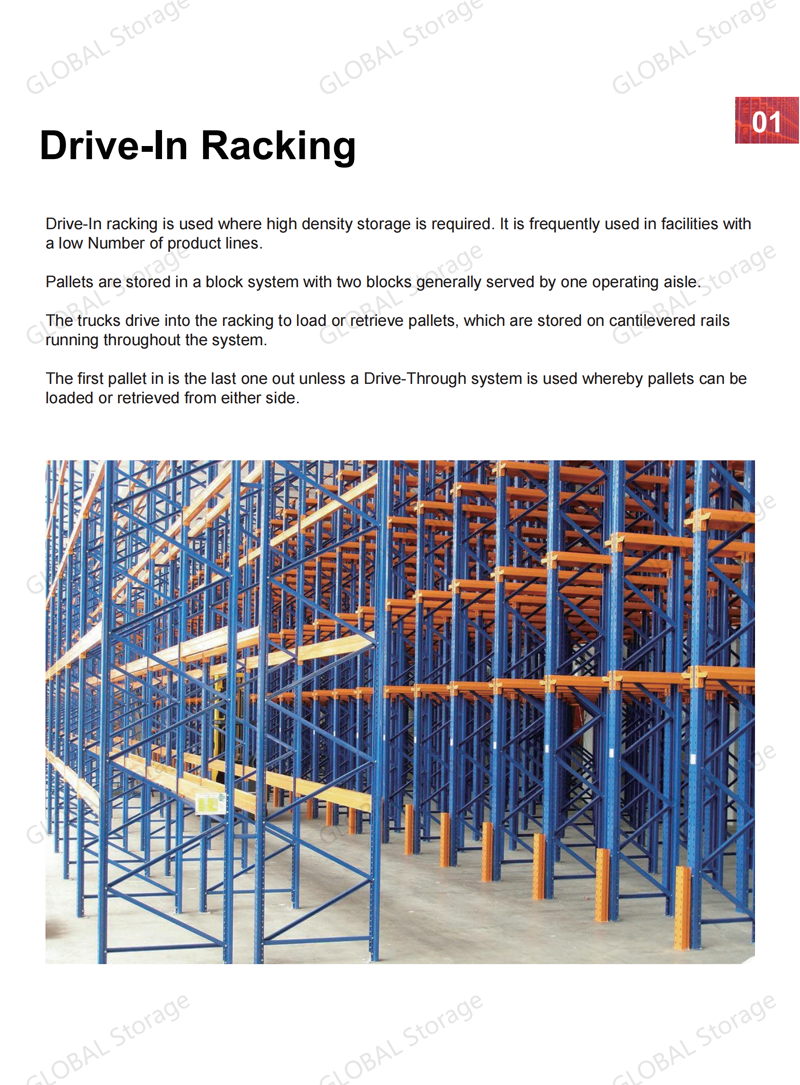
1. Introduction to Drive In Racking System
The Drive In Racking System is a type of high - density pallet storage system. It is designed to maximize the cubic space within a warehouse by minimizing the number of operating aisles required for forklifts. This system is an excellent choice for storing a large number of unit loads of the same product reference.
1.1 Structure and Design
The system consists of a series of uprights that are connected to form parallel aisles inside the structure. These aisles are equipped with load support rails on both sides at different levels. Pallets are placed on these rails. The forklift enters the racking structure and deposits or retrieves pallets at a height higher than the level where they will be placed. The uprights are often made of high - strength steel to support the weight of the pallets and withstand the impact of forklift operations.
2. Types of Storage in the Compact System
2.1 Drive In Pallet Racking (LIFO - Last in, First out)
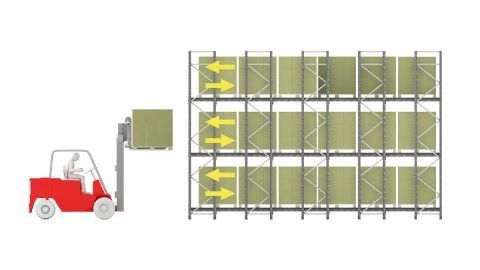
This is the most common type of compact racking system. In a Drive In Pallet Racking setup, there is only a single access aisle for the forklift. The forklift enters the aisle and loads pallets from the front to the back. When it comes to retrieval, the last pallet that was loaded is the first one to be taken out. This LIFO method is highly suitable for warehouses where the material turnover is low. For example, in a factory that stores raw materials for seasonal production, the Drive In Pallet Racking with LIFO can be an ideal choice as the raw materials are not frequently accessed, and the system allows for maximum space utilization.
2.2 Drive Through Pallet Racking (FIFO – First in, First out)
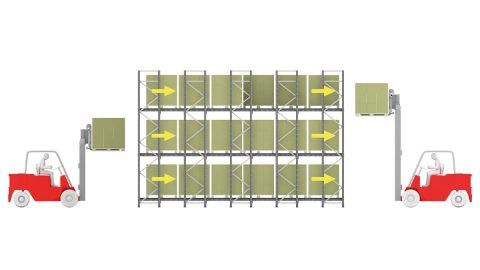
The Drive Through Pallet Racking system requires two accesses, one on each side of the racking. Forklifts can enter from one side to load pallets and exit from the other side to unload them. This setup follows the FIFO method, where the first pallet that is loaded is the first one to be retrieved. It is an excellent system for high - turnover products. In a food distribution center, for instance, where products have a short shelf life and need to be rotated quickly, the Drive Through Pallet Racking can ensure that the oldest products are shipped out first, reducing the risk of spoilage.
3. Advantages of the Drive In Racking System
3.1 High - Density Storage
One of the primary advantages of the Drive In Racking System is its ability to provide high - density storage. By reducing the number of operating aisles, it can increase the storage capacity of a warehouse by up to 80% - 90% compared to selective pallet racking. This is especially beneficial for businesses that have limited warehouse space but need to store a large volume of goods.
3.2 Cost - Effective
The system is cost - effective in several ways. Firstly, the reduced need for operating aisles means that more storage space can be created within the existing warehouse footprint, eliminating the need for costly warehouse expansions. Secondly, the simplicity of the design, with fewer components compared to some other racking systems, reduces manufacturing and installation costs. Additionally, the ability to store more goods in a smaller space leads to lower overall storage costs per unit.
3.3 Excellent Stock Control
Each lane in the Drive In Racking System is dedicated to a specific product reference. This makes it easy for warehouse managers to keep track of inventory. They can quickly identify which lane contains a particular product and how many pallets are available. This level of organization is particularly useful for businesses that deal with a large number of pallets of the same product.
3.4 Versatility
The Drive In Racking System can be customized to suit different types of products and storage requirements. The height and depth of the racks can be adjusted according to the size of the pallets and the available warehouse space. It can also be used in various industries, including food and beverage, manufacturing, and cold storage.
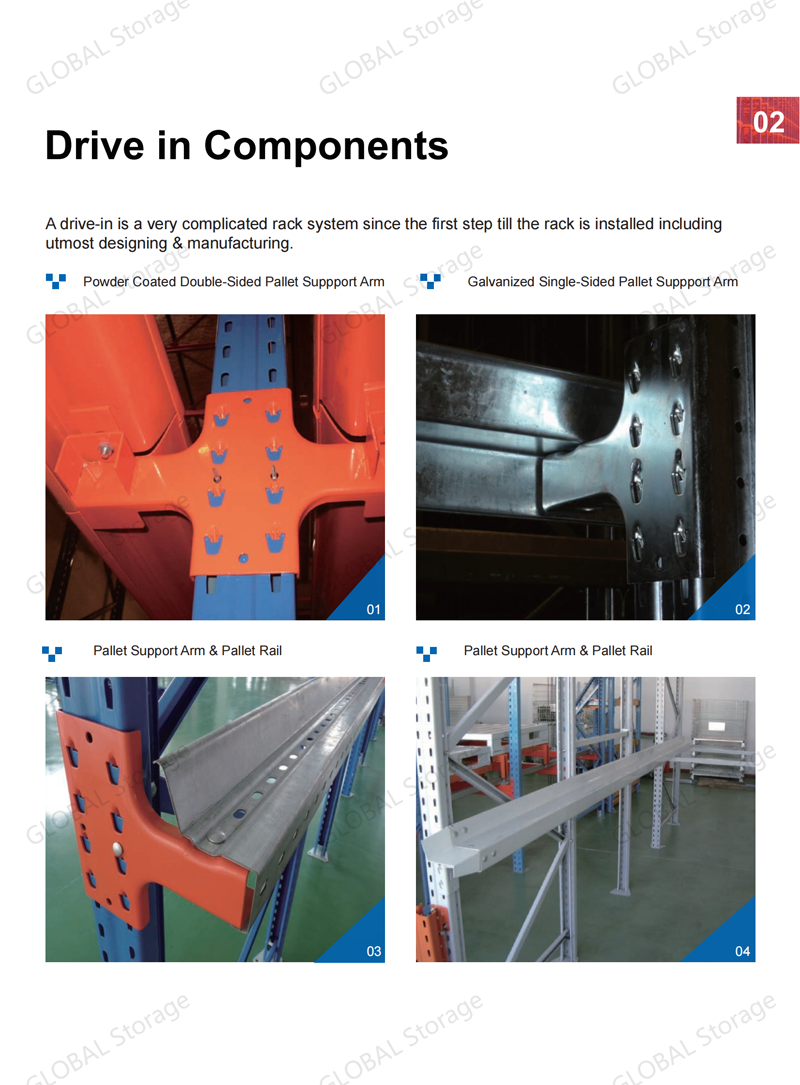
4. Applications of the Drive In Racking System
4.1 Cold Storage
Cold storage facilities often have high construction and operating costs. The Drive In Racking System is well - suited for such environments as it maximizes the use of the limited and expensive space. For example, in a frozen food warehouse, the system can store a large number of pallets of frozen products, ensuring that the cold air circulation is optimized and the storage capacity is fully utilized.
4.2 Manufacturing
Manufacturing plants often need to store large quantities of raw materials or finished products. The Drive In Racking System can be used to store these items efficiently. For instance, a furniture manufacturing company can use the system to store large sheets of plywood or lumber, which are typically stored in large quantities and do not require frequent access.
4.3 Retail Distribution Centers
Retail distribution centers receive and ship large volumes of products. The Drive In Racking System can be used to store products that are not time - sensitive and are sold in large quantities. This allows the distribution center to make the most of its storage space and improve the overall efficiency of its operations.
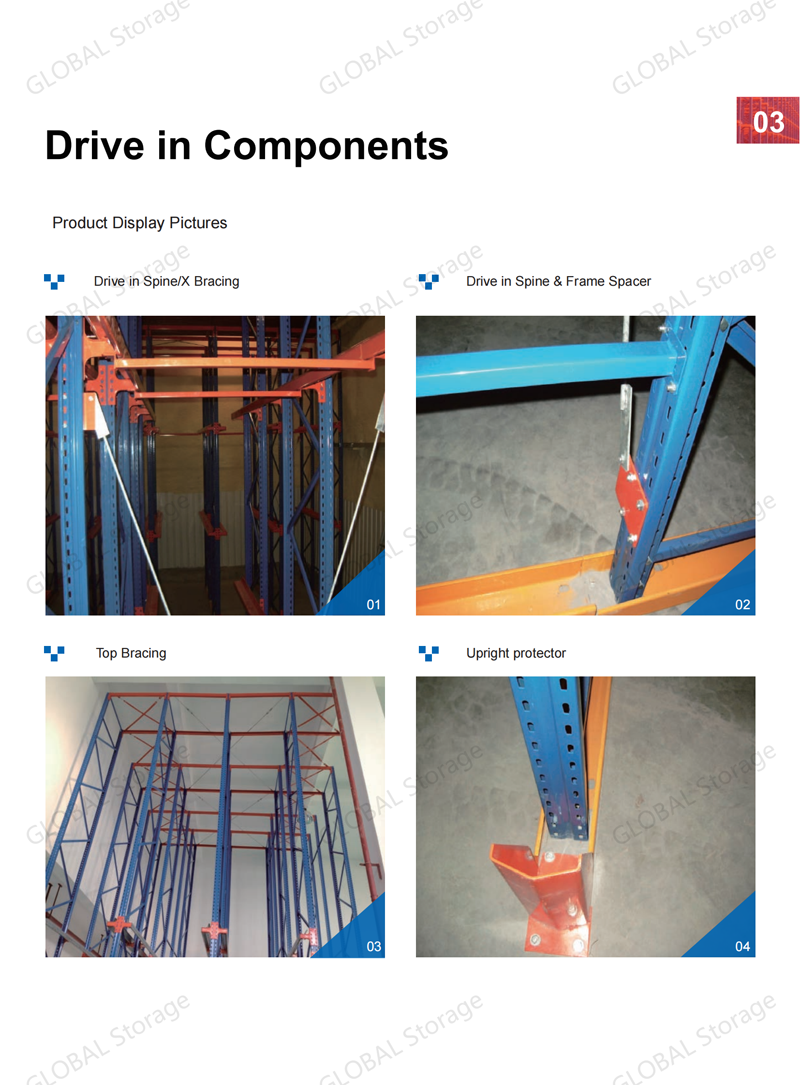
5. Considerations When Implementing a Drive In Racking System
5.1 Forklift Compatibility
The type of forklift used in a Drive In Racking System must be carefully selected. The forklift should be able to maneuver within the narrow aisles of the racking structure safely. It should also have the appropriate lifting capacity to handle the pallets. Additionally, the driver of the forklift needs to be trained to operate in the specific environment of the Drive In Racking System to avoid collisions and ensure safe and efficient operations.
5.2 Safety Measures
Safety is of utmost importance when using a Drive In Racking System. The system should be equipped with safety features such as post protectors to prevent forklifts from damaging the uprights, and floor guide rails to help the forklift driver navigate the aisles safely. Regular inspections of the racking system should be carried out to check for any signs of wear or damage, and any issues should be addressed promptly.
5.3 Product Characteristics
The nature of the products being stored also needs to be considered. For example, if the products are fragile or have a short shelf life, the appropriate type of Drive In Racking (LIFO or FIFO) should be selected. Additionally, the weight and size of the pallets and the products should be within the capacity limits of the racking system.
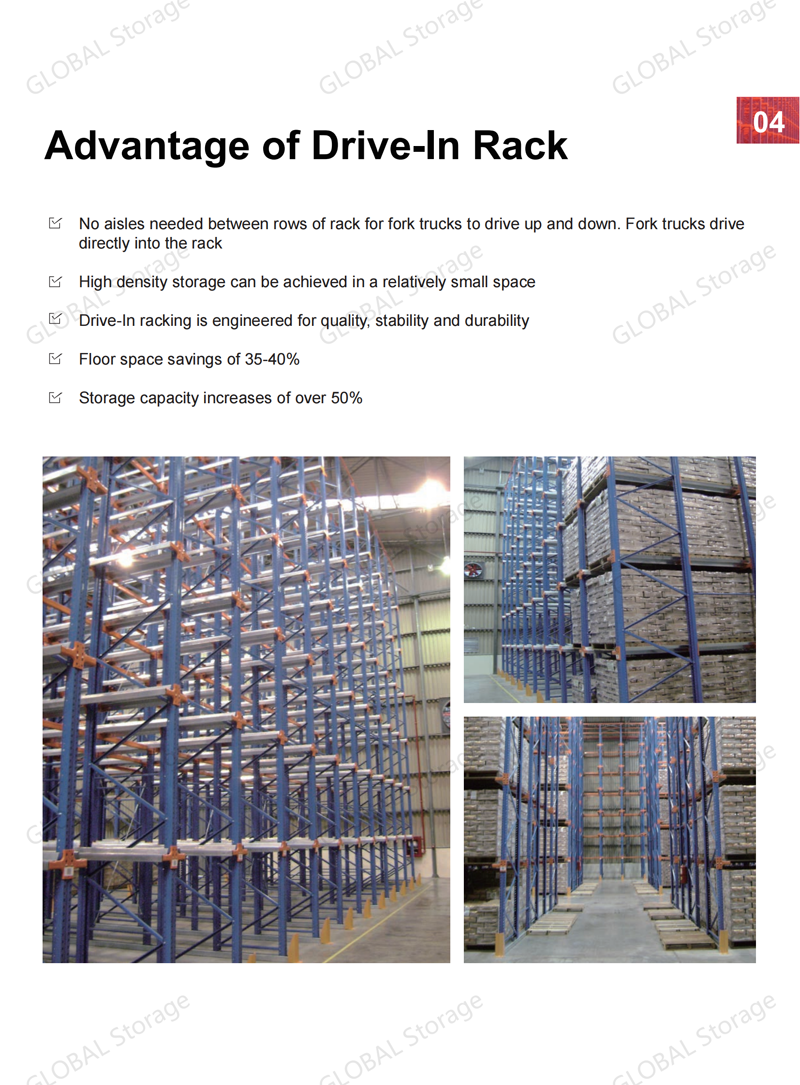
In conclusion, the Drive In Racking System offers a highly efficient and cost - effective solution for high - density storage. By understanding its types, advantages, applications, and considerations, businesses can make informed decisions on whether this system is the right fit for their warehousing needs.
To know more please contact us.Email:[email protected]